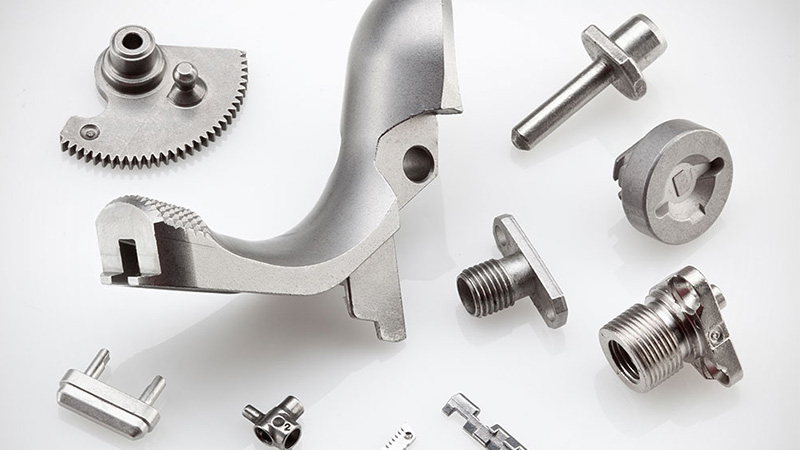
MIM – Metal Injection Molding
Metal injection molding or MIM is a process where fine powdered metal is injected into a mold allowing for high volume complex parts. The injection process is similar to pressure die casting. MIM is typically used for small size complex parts that would otherwise require a great deal of machining or assembly. MIM typically has good dimensional control.
- Materials: Stainless Steel , Nickel Steel, Tool steel, Titanium and more.
- Up to 4 inch diameter
Capabilities
- Material: Case hardened steel: MIM8620, 9310, 4600
Through hardened steel: MIM 4650, 4340, 4140, 52100
Stainless steel: SS17-4ph, 304L, 420
High Temp. App: 440C, 310Nb, 310
Corrosion Resistant: SS316L, 310Nb
Magnetic material: Fe3Si, SS430, Fe-49Co-2V
Heavy / Super Alloy: WHA1, WHA2, Inconel, Nimonic90
Tool steel: S7, M2, D2 - Weight limit: <200 gm
Ideal is 0.1 – 50 gm - Length limit: 7.8 in
Ideal is < 2.5 in - Wall thickness: 0.02 – 0.2 in
- Tolerances per ISO 2768 (m)
Rule of thumb is +/- 0.5% of nominal dimension - ISO 9001-2008, ISO/TS 16949:2009, ISO/13485:2003, AS 9100 Rev. C
Understanding Metal Injection Molding
Metal Injection Molding (MIM) gives the strength and integrity of a machined metal part while giving the versatility of plastic injection molding.
The Metal Injection Molding Process:
The MIM process combines fine metal powders with plastic binders. This allows the metal to be injected into a mold using similar equipment as standard plastic injection. The part is referred to as a “green part” after it is molded but before the binders are removed. The“green part” must have the binders removed through a thermal process. The metal part is then sintered at a temperature to bind the particles but not melt the metal. Metal injection molded parts are up to 98% as dense as wrought iron. They are used in a broad range of applications (including medical, dental, firearms, aerospace, and automotive.)
Metal injection molding is best used for complex small parts. Tolerances as small as +/-. 003″ per inch can usually be held without secondary processes. The difficulty of fabrication through other means may make it inefficient or even impossible to manufacture otherwise. Increasing complexity for traditional manufacturing methods typically does not increase cost in a metal injection molding operation due to the wide range of features possible through injection molding (internal and external threads, miniaturization, branding).
The MIM process offers the capability to realize parts closer to net shape to help avoid secondary operations.
As the process is based on injection, very complex parts with tight tolerances and a density of more than 98% can be considered. It is easy to produce large numbers of parts at attractive prices. The cost of the part is directly related to its weight and its volume.
This process is to be able to produce parts from 50 to 500 grams. or more, with tight tolerances.
The usual limits are: +/- 0.5% of the dimension and could be reduced to +/- 0.3% on target dimensions.
If you have any questions or would like to request a quote, contact us today.